Project 4 (Efficient Lightweight Actuation) focusses on developing a new generation of actuators for implementation in wearable robotic devices. Wearable robotic applications share common design goals like low mass and high compactness and efficiency, but also have unique requirements regarding their output characteristics (e.g. speed and torque). A large part of the actuators that will be created in this project are intended for support of individuals with disabilities (like Duchene muscular dystrophy and spinal cord injury). This places additional requirements on design and testing of the actuators in order to comply with regulations for medical devices. The developers aim to make a contribution to by creating:
- A simulation software that facilitates easy selection of actuator components and optimization based on required characteristics of an application;
- an actuator design that is relatively easy to scale to the power and size requirements of an application;
- actuator hardware that can be used in the application projects (6-8) of the program;
- testing facilities that are needed to calibrate actuators, evaluate their performance and execute tests that shown compliance to the safety standards.
The working principle of the actuator is based on a previous generation of actuators built for the Symbitron Exoskeleton. For the new generation of actuators developed in this project, the focus is on design for assembly and maintenance, and – more importantly – increased robustness of the electronics. The goal is to maximize the time that researchers can spend on the experiments in the application projects without worrying about robustness of the actuator.
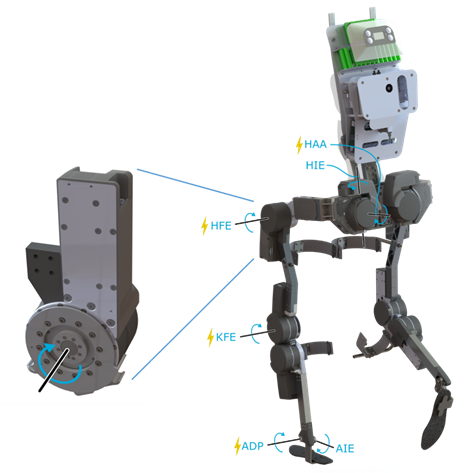
During the first period of the project, two actuator have been developed: the big actuator for use in lifting aid in project 8 and the small actuator for an active arm exoskeleton in project 7.
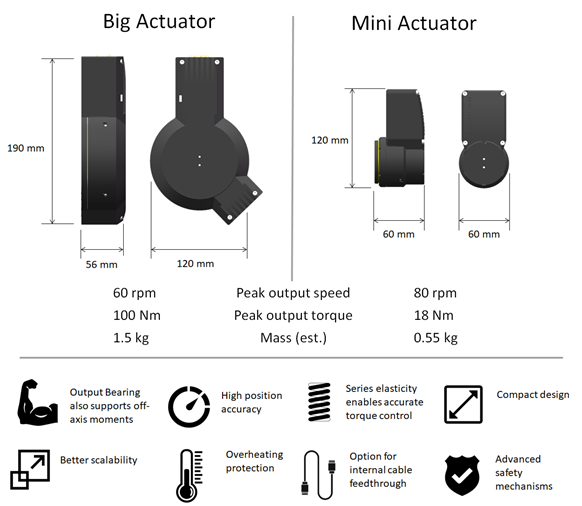
The drivetrain contains a spring in series. The spring’s primary function is measuring the output torque of the actuator (by measuring deflection of the spring), but also protects the drivetrain from shocks and vibrations. The actuator output characteristics can be changed by changing the motor type and gearbox ratio. The actuator presented here includes a harmonic drive gearbox. These gearboxes have poor energy efficiency and have limited possibilities for application depend optimization. The coming year, the we will start focusing on the Archimedes drive, which has the potential to overcome these limitations. For more information visit imsystems.nl